On-the-Go Fixes: A Guide to Common Mobile Truck Repairs
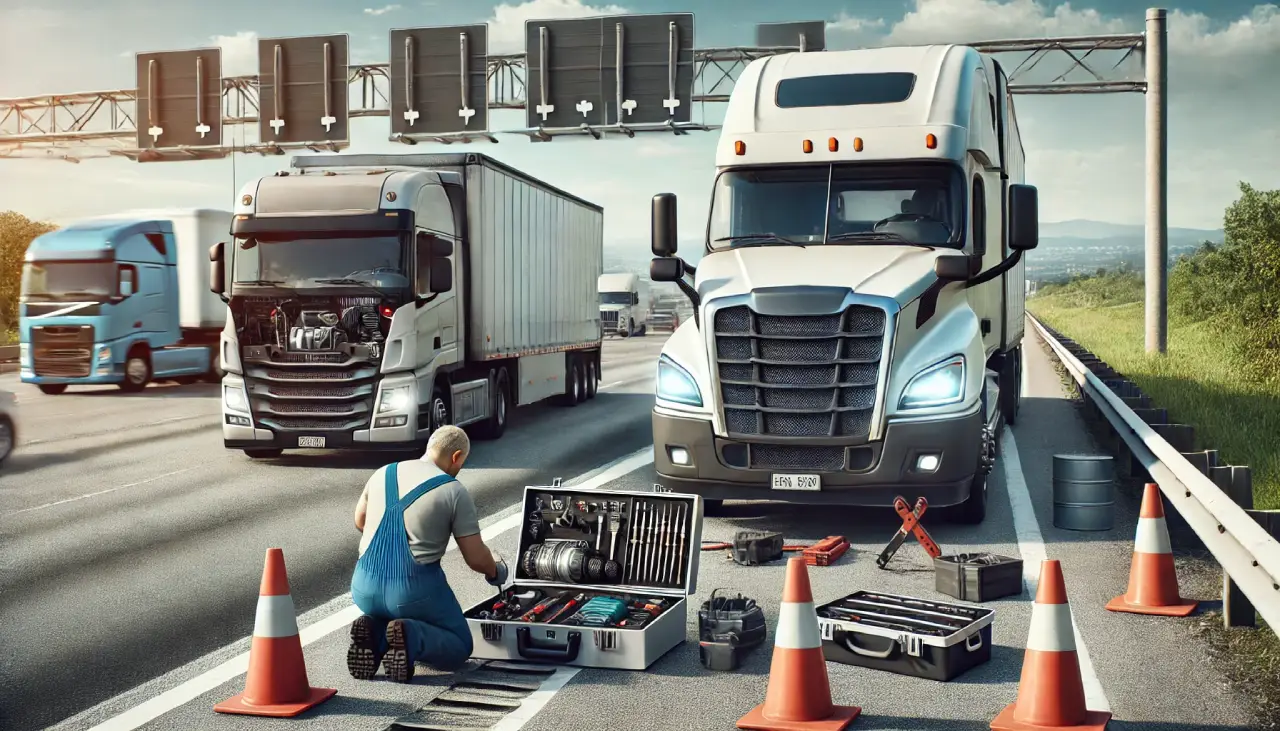
Keeping a commercial truck in peak condition is crucial for safety, efficiency, and profitability. However, even the most well-maintained trucks can experience issues on the road. This guide will cover six common areas of mobile truck repairs, providing practical advice to address these problems swiftly and effectively.
To learn more about our mobile repairs at Pacific Fleet Services, please visit our Mobile Truck Repair page here.
Tire and Wheel Repairs
Tire and wheel issues are among the most frequent problems truck drivers encounter. Common issues include:
- Flat tires
- Worn-out treads
- Damaged rims
- Uneven tire wear
To tackle these, it's essential to have the right tools on hand, such as a jack, lug wrench, spare tires, tire pressure gauge, patch kits, portable air compressors, and tire rotation tools.
When faced with a flat tire, ensure the truck is parked on a flat surface before using the jack to lift it. Remove the flat tire with a lug wrench, mount the spare, and tighten the lug nuts in a star pattern to ensure even pressure. If a puncture is small and the tire is still in good condition, a patch kit can be used to seal the hole, followed by inflating the tire with a portable air compressor.
Maintaining proper tire pressure is critical for safety and fuel efficiency. Regularly check the pressure using a gauge and adjust as needed to match the manufacturer’s recommended PSI. Additionally, performing tire rotations every 6,000 to 8,000 miles helps to ensure even tire wear, prolonging the lifespan of the tires. Preventive measures like regular inspections for damage, proper inflation, and scheduled rotations can significantly reduce the risk of tire-related issues.
Battery and Electrical System Maintenance
Battery and electrical system failures can halt a truck’s operations, making it imperative to address these issues quickly. Common problems include:
- Dead batteries
- Corroded terminals
- Faulty alternators
- Blown fuses
- Dimming lights
Essential tools for these repairs include a multimeter, battery charger, jumper cables, terminal cleaner, spare fuses, and wiring kits.
If the battery dies, jump-starting is a quick fix. Connect the jumper cables to the dead battery and a charged one, start the truck, and let it run for a few minutes to charge the battery. For a more permanent solution, replacing an old battery involves disconnecting the negative and positive terminals, removing the old battery, and installing a new one. Corroded terminals can be cleaned using a terminal cleaner, and a protective coating can prevent future corrosion.
To troubleshoot electrical problems, use a multimeter to check the voltage output of the alternator. If it does not provide the correct voltage, it may need replacing. Blown fuses can be replaced with spares, and faulty wiring can be repaired with a wiring kit. Regular inspections of the battery and terminals, keeping them clean, and routinely checking electrical connections can prevent many electrical issues from arising.
Engine and Mechanical Troubleshooting
Engine and mechanical problems can range from minor inconveniences to major breakdowns. Common issues include:
- Overheating
- Oil leaks
- Broken belts
- Unusual noises
The necessary tools for these repairs include wrenches, screwdrivers, oil, coolant, spare belts, a diagnostic scanner, and leak detection kits.
To keep the engine running smoothly, regularly check and top off fluids like oil and coolant. If you notice oil leaks, use a leak detection kit to find the source and repair or replace the affected components. Broken belts are a common cause of mechanical failure; inspect them regularly and replace any that show signs of wear.
A diagnostic scanner can be invaluable for identifying engine issues. By connecting it to the truck’s computer system, you can retrieve diagnostic codes that indicate specific problems. Address these issues promptly to prevent more significant damage. Regular fluid checks, visual inspections of the engine, and adherence to scheduled maintenance routines are key preventive measures to avoid engine and mechanical problems.
Brake System Repairs
Brake system failures are serious and can lead to dangerous situations on the road. Common brake issues include:
- Worn brake pads
- Faulty brake lines
- Squeaky brakes
Essential tools for brake repairs include brake pads, wrenches, a brake bleeder kit, and brake cleaner.
To inspect and replace brake pads, remove the wheel and examine the pads for wear. If they are below the minimum thickness, replace them with new ones. Bleeding the brake lines using a brake bleeder kit removes air from the system, ensuring the brake pedal feels firm.
If brakes are squeaking, use brake cleaner to remove dirt and debris, and inspect for worn components that might be causing the noise. Regular brake inspections, maintaining proper fluid levels, and timely replacement of worn components are crucial for ensuring the braking system functions correctly.
Coolant System Maintenance
The coolant system is vital for preventing the engine from overheating. Common issues include:
- Radiator leaks
- Overheating
- Coolant loss
- Faulty thermostats
Necessary tools for these repairs include coolant, radiator sealant, thermostat, hose clamps, and a pressure tester.
Regularly check the coolant levels and top off with the appropriate coolant mixture to ensure the engine stays cool. If you notice radiator leaks, use radiator sealant for a temporary fix, but replace damaged hoses and clamps as soon as possible. Inspect hoses regularly for wear and replace them if necessary. If the thermostat is malfunctioning, it will need replacing to ensure proper coolant flow.
Flushing the cooling system periodically helps remove debris and old coolant, maintaining the system’s efficiency. Regular checks of coolant levels, hose inspections, and radiator maintenance are essential preventive measures to avoid overheating and coolant system failures.
Lighting and Signal Repairs
Proper lighting and signaling are crucial for safety, especially during nighttime driving and adverse weather conditions. Common issues include:
- Burnt-out bulbs
- Faulty wiring
- Dim lights
- Non-functional signals
Tools needed for these repairs include replacement bulbs, wiring kits, a multimeter, screwdrivers, and fuses.
To replace burnt-out bulbs, remove the cover, take out the old bulb, and install a new one. If the lights are dim, check the wiring and use a multimeter to ensure there is adequate voltage. Repair any faulty wiring with a wiring kit. Non-functional signals can often be fixed by replacing blown fuses and ensuring all connections are secure.
Regular inspections of lights and signals, keeping spare bulbs on hand, and ensuring connections are clean and secure can prevent lighting and signal problems from occurring. Maintaining a well-functioning lighting system is essential for safe driving and compliance with road regulations.
Final Thoughts
By following this guide, truck drivers can handle common repairs on the go, ensuring their vehicles remain operational and safe. Regular maintenance and being prepared with the right tools can minimize downtime and keep your trucks on the road.
Contact Us
For reliable and efficient Pacific Fleet services, we are here to serve you. Our team of skilled technicians specializes in heavy-duty diesel repair, providing trustworthy and dependable solutions to keep your fleet operating smoothly. After hours and weekend Appointments available.